Some of Nigeria’s main cement producers have seen earnings rise on the back of strong demand, but although sustained consumption growth is forecast for the near term, challenges remain in the form of high logistics costs.
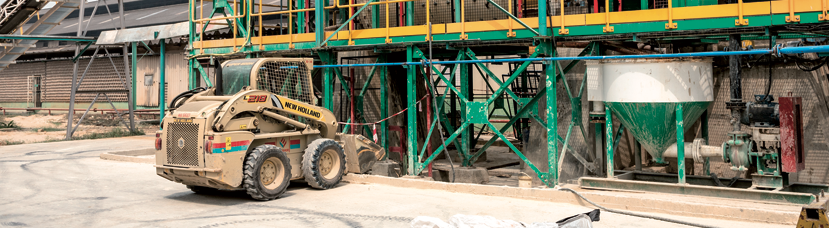
Accounting for more than 60% of market share, Dangote Industries saw sales rise by 13.9% year-on-year in the first half of 2018, with 7.3m tonnes delivered domestically and a further 500,000 tonnes of output exported, driving revenue up more than 18%.
Meanwhile, Lafarge Africa’s Nigeria operations posted a 22% increase in production volume, largely due to exports to Ghana that started in the fourth quarter of 2017. The group recorded profit of N1.9bn ($6.1m) in the second quarter, shrugging off concerns over inflationary pressure and a weak exchange rate.
In its first half report, Lafarge said the full-year outlook for the cement market remained favourable, underpinned by signs of recovery since March, with expectations of solid performance in the second half and beyond supported by improved demand and the strengthening of the logistics chain.
Indicators point to rise in consumption
These results appear to be in line with forecasts for the segment published in February by the research department of financial services firm RMB Nigeria, which projects consumption to rise by 7% this year, reversing the 17% contraction recorded in 2017. According to the company, the increase will be driven by the construction of concrete roads and efforts to address the housing deficit, which together could account for 77m tonnes of cement demand through to 2020.
Meanwhile, a recent upswing in demand was indicated in the Central Bank of Nigeria’s latest purchasing managers’ index, released on July 31, which saw the sub-index for new cement orders rise 12.5 points month-on-month (m-o-m) to 62.5.
The large increase reversed the flat growth seen since March, when new cement orders doubled m-o-m to 50 points.
Consolidation on the cards
As firms look to capitalise on the positive growth outlook, merger and acquisition (M&A) activity is picking up. Last month Cement Company of Northern Nigeria (CCNN), owner of a newly commissioned 1.5m-tonne-per-annum factory at Sokoto, announced plans to merge with Kalambaina Cement, a wholly owned subsidiary of BUA Cement.
The proposed merger, which is contingent on regulatory and shareholder approval, is expected to create a firm with a combined production capacity of 2m tonnes per annum.
There are also indications there could be M&A activity among the market’s larger firms next year. Edwin Devakumar, the executive director of Dangote Group, said in early July 2018 that the company has likely gone as far as it can by building operations from the ground up, and pointed to acquisitions as a route to further growth.
The company has suggested the possibility of listing on the London Stock Exchange in 2019, which could serve to raise further capital to fund M&A activity.
Infrastructure gap poses opportunities, challenges
Prospects for cement producers could be further buoyed should the government be successful in attracting private investors to a series of big-ticket infrastructure projects, which will be exhibited at the Africa Investment Forum held by the African Development Bank (AfDB) in November.
At the event, which aims to accelerate private investment in Africa, Nigeria will showcase a series of infrastructure developments, including a bus rapid transit system for Abuja and a gas commercialisation project, among others.
The AfDB will work with the government, institutions and the private sector to prepare the projects, focusing on improving profitability and lowering risk profiles.
Overall, the bank estimates that Nigerian infrastructure needs up to $3trn in investment over the next 22 years, making involvement from private players key, and offering cement producers opportunities for further growth.
In the interim, however, gaps in the transport network will likely continue to generate additional costs for cement players, squeezing margins.
The expense of shipping cement around the country can add up to N14,000 ($45) per tonne, comprising as much as one-third of production costs, according to Abdulsamad Rabiu, chairman and CEO of BUA Group. Much of this is due to the lack of a strong logistics network, with transport capacity limited by poor roads and shortfalls in rail links, he told local media in August.